Insights
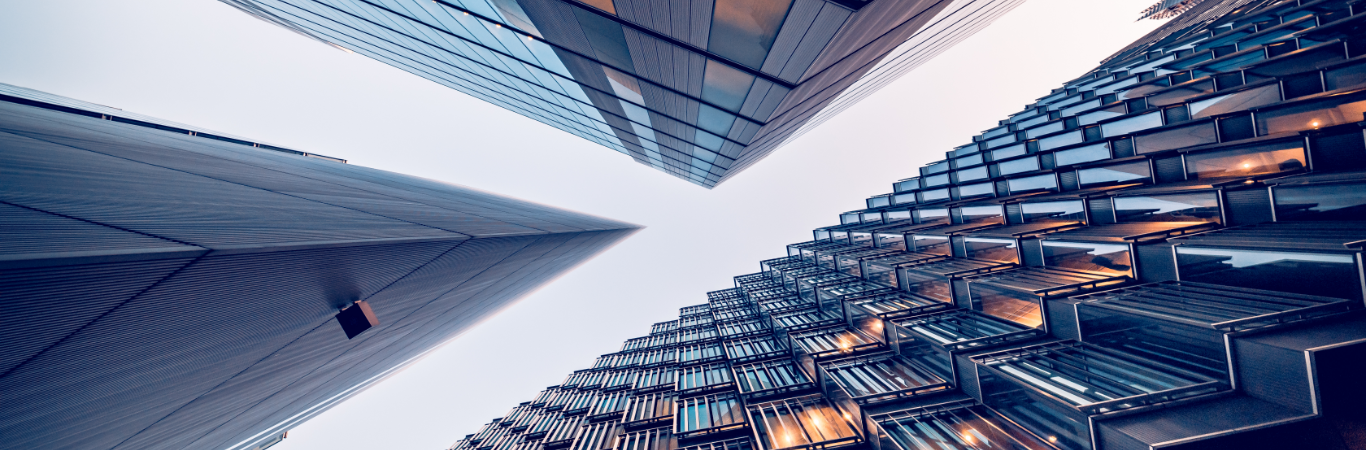
Explore our strategic insights and gain new perspective on industry trends.
Article
Construction Sector Evolution Is Driving Changes in Equipment Finance
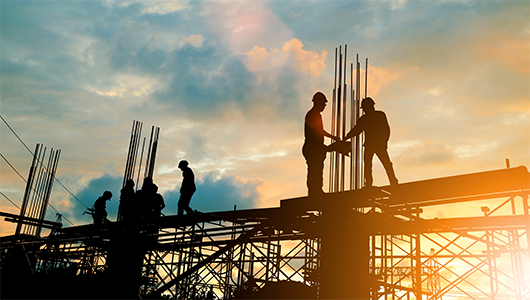
As construction spending rises and project needs evolve, equipment finance is transforming—creating new investment opportunities and reshaping how lender support this dynamic, capital-intensive sector.
Featured
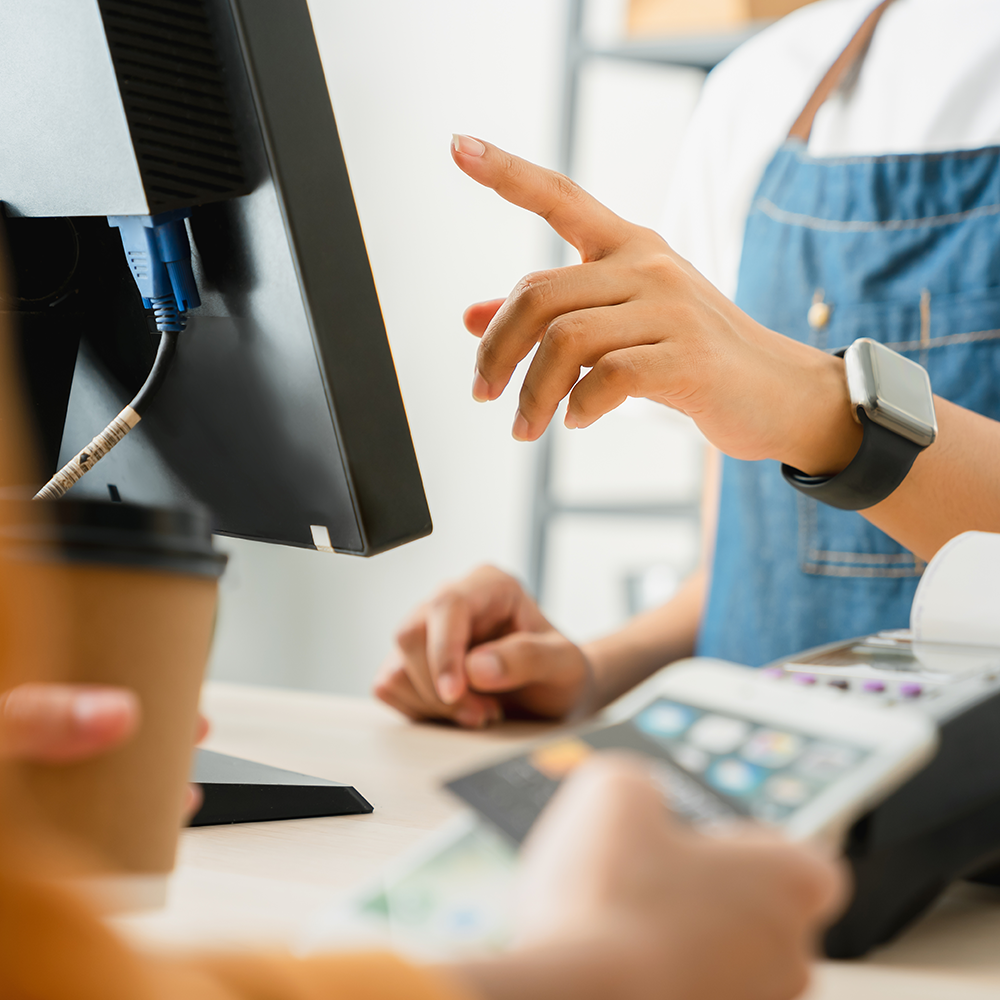
Article
U.S. Holiday Sales Forecasted to Modestly Increase Amid Economic & Political Uncertainty
Gordon Brothers forecasts U.S. retail sales will modestly increase 1.2% to 3.5% this holiday season relative to last year.
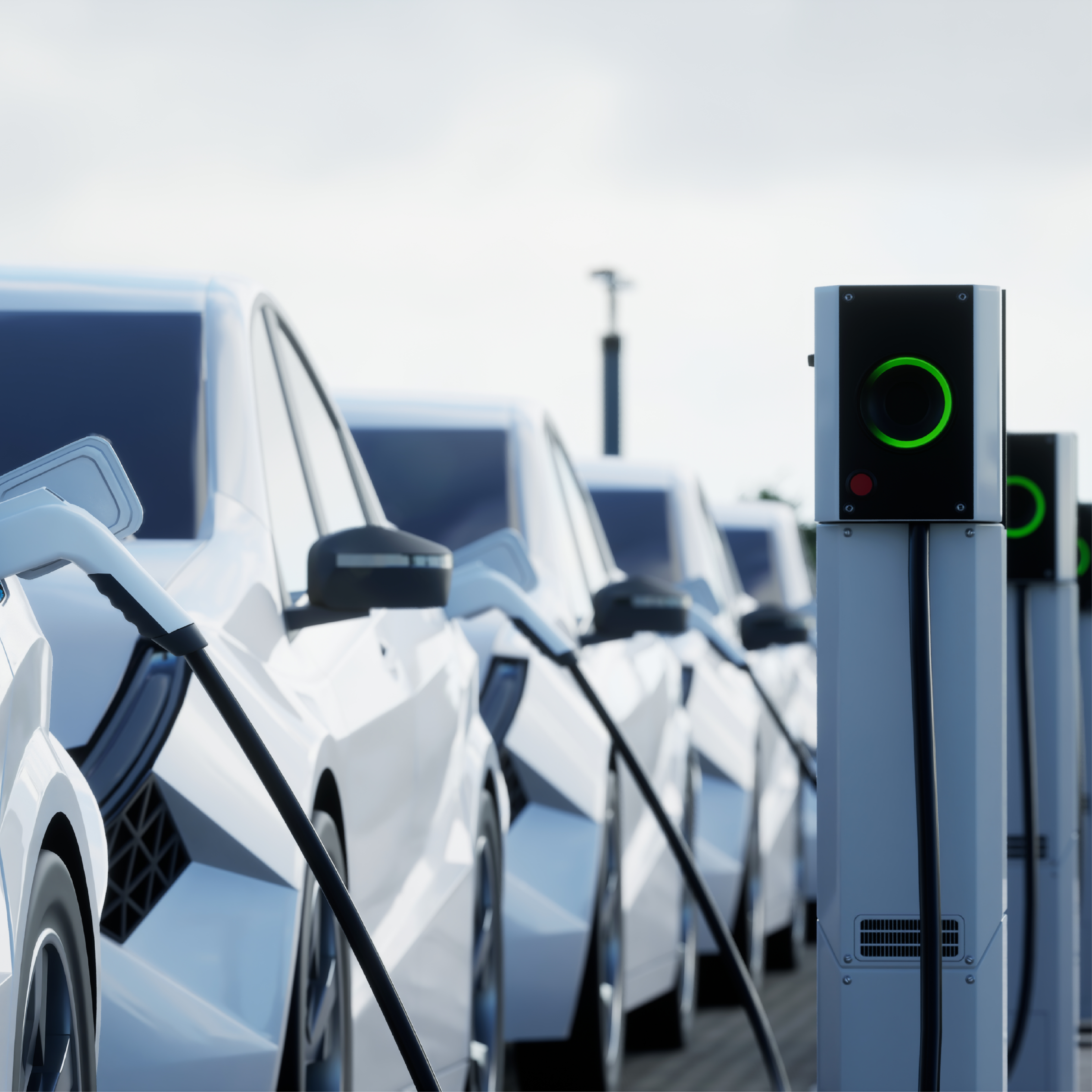
Video
Navigating Complexity and Change in the Current EV Landscape
Our experts explore industry challenges, what the future holds and implications for both consumers and businesses.
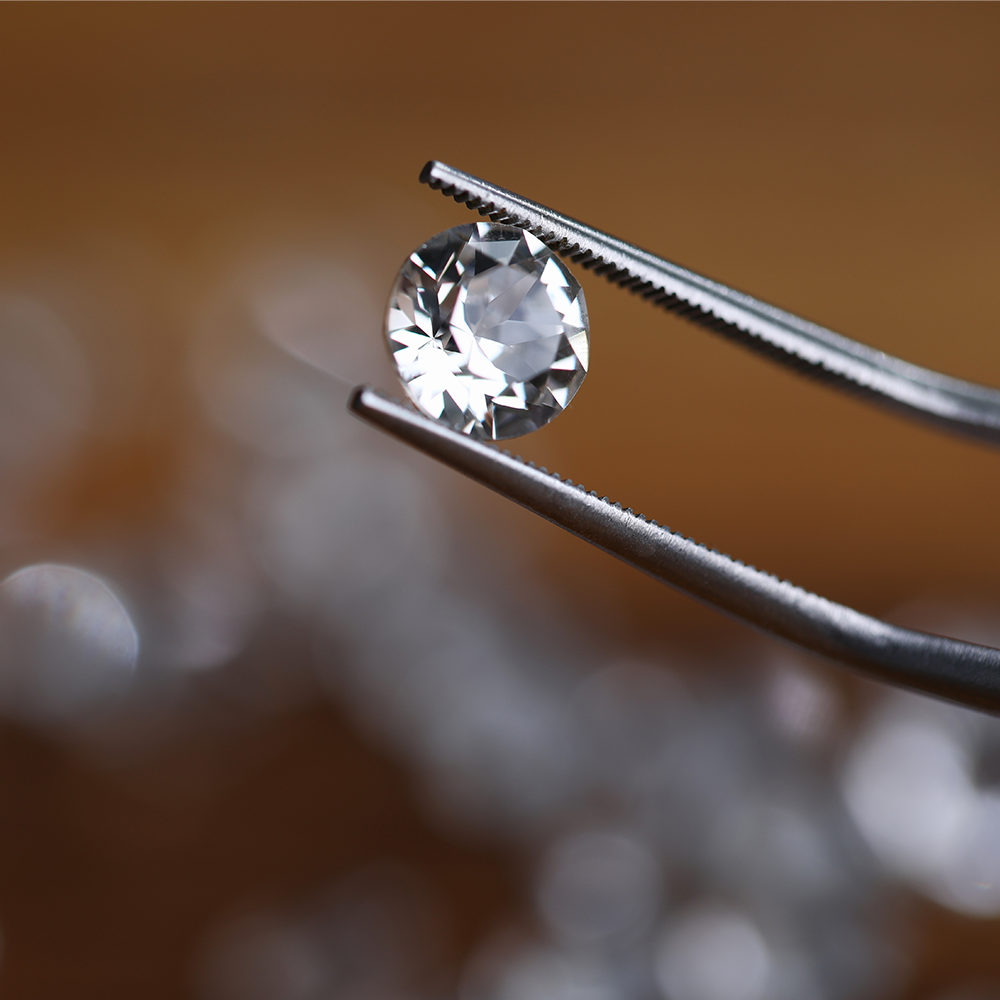
Article
The Rise of Lab-Grown Diamonds: A Multifaceted Challenge for Jewelers
Gordon Brothers explores how the emergence of manufactured stones is rearranging industry economics.
-
Asset Services
-
Asset Trading
-
Asset Lending & Financing
-
Brands
-
Commercial & Industrial
-
Retail
-
Real Estate
-
Aerospace & Defense
-
Agriculture
-
Automotive
-
Chemicals
-
Construction
-
Electronics & Technology
-
Energy
-
Food & Beverage
-
Forestry Products
-
Health Care & Pharmaceuticals
-
Life Sciences
-
Machinery & Equipment
-
Manufacturing
-
Marine
-
Mining
-
Mobile Modular
-
Oil & Gas
-
Plastics
-
Printing
-
Textiles & Apparel
-
Transportation
-
Waste Management
-
Apparel & Accessories
-
Auto Parts & Accessories
-
Beer, Wine & Spirits
-
Books, Music & Video Games
-
Consumer Electronics & Appliances
-
Cosmetics & Fragrances
-
Department Stores
-
Digital Commerce
-
Discount & Dollar Stores
-
Drug Stores
-
Footwear
-
Furniture & Housewares
-
General Merchandise
-
Grocery
-
Home Improvement
-
Jewelry
-
Office Supplies
-
Restaurant
-
Sporting Goods
-
Store Furniture & Fixtures
-
Store Leases
-
Toys
-
United States
-
Germany
-
Italy
-
Middle East
-
Spain
-
United Kingdom
-
Australia & New Zealand
-
Japan
-
Singapore
-
South East Asia
-
Article
-
Infographic
-
Podcast
-
Video
-
Webinar Recording
Insights delivered right
to your inbox.
Sign up to receive insights, event information
and company news.